Enhancing Manufacturing Efficiency with Precision Plastic Parts
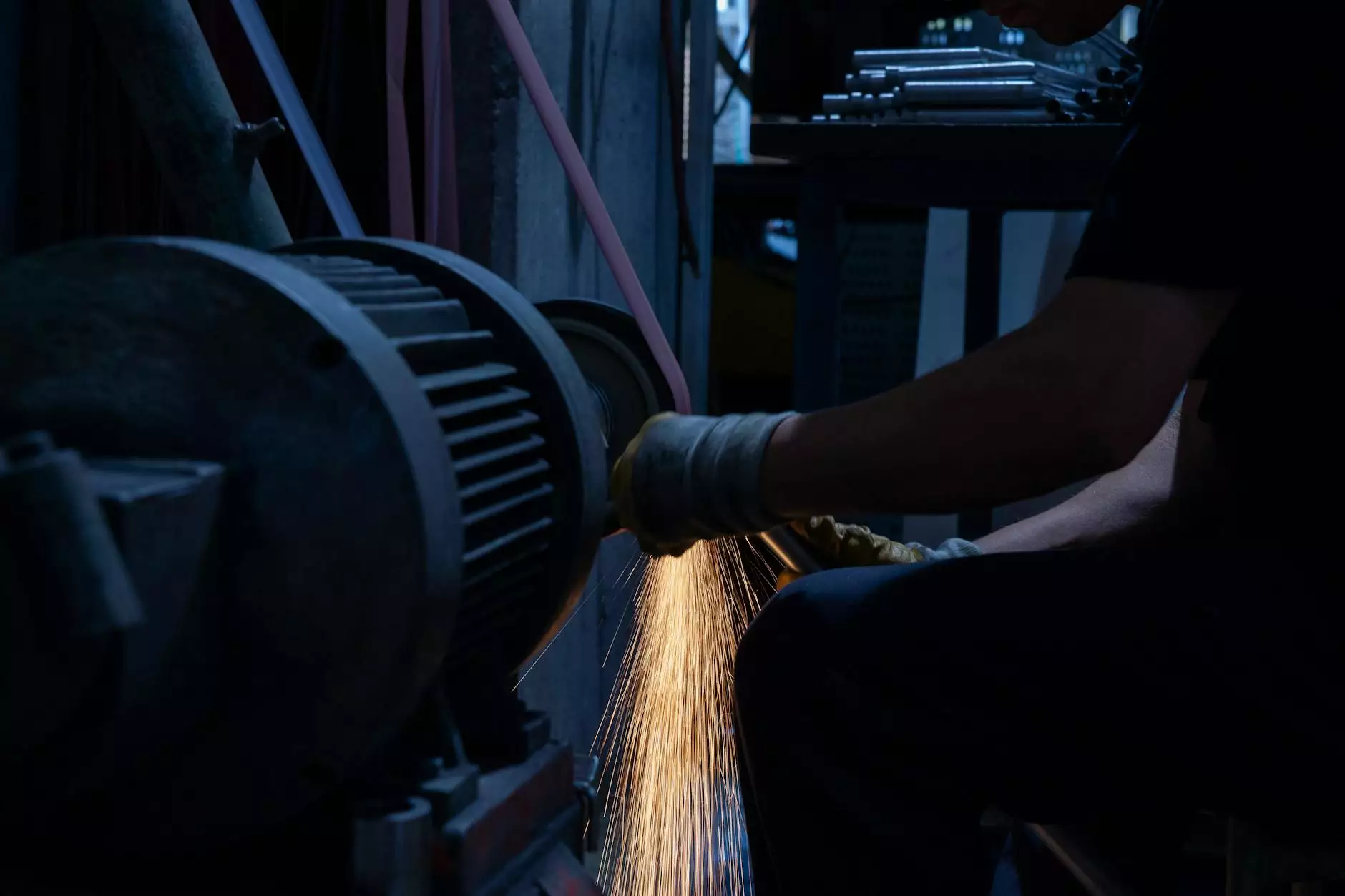
The manufacturing landscape is continually evolving, with technological advancements leading to increased demands for precision plastic parts. As industries seek higher efficiency, reduced costs, and improved product quality, understanding the role of these parts becomes essential. This article delves deep into the world of precision plastic manufacturing, its benefits, applications, and future trends.
What Are Precision Plastic Parts?
Precision plastic parts refer to components manufactured from plastic materials with high accuracy to meet specific design specifications. These parts play a vital role in various industries, including automotive, healthcare, electronics, and consumer goods. The manufacturing process involves advanced techniques such as injection molding, CNC machining, and additive manufacturing, which contribute to their accuracy and reliability.
The Importance of Precision in Manufacturing
In today’s competitive market, precision in manufacturing is crucial. Here are a few reasons why:
- Quality Assurance: High precision leads to better quality products that meet or exceed customer expectations.
- Cost Efficiency: Precise components reduce waste and the need for rework, thereby saving costs in production.
- Enhanced Performance: Components that fit perfectly function better, resulting in improved product reliability and longevity.
- Innovation: Precision allows for complex designs that can lead to innovative products and solutions.
Benefits of Using Precision Plastic Parts
The use of precision plastic parts offers numerous advantages, including:
1. Lightweight and Durable
Plastic parts are significantly lighter than their metal counterparts, making them ideal for applications where weight is a concern. Additionally, modern plastics can be engineered to withstand harsh environments, providing durability without the added weight.
2. Cost-Effective Manufacturing
While initial setup costs for precision manufacturing can be high, the overall cost savings in production processes, reduced material waste, and lower shipping costs make precision plastic parts a cost-effective choice in the long run.
3. Flexibility in Design
Precision engineering enables designers to create complex shapes and intricate details that are not possible with traditional materials. This flexibility fosters creativity and innovation in product design.
4. Resistance to Corrosion and Chemicals
Many modern plastics are resistant to chemicals and corrosion, making them suitable for various applications, especially in industries like healthcare and automotive, where exposure to harsh substances is common.
5. Reduced Lead Times
Advanced manufacturing technologies, such as 3D printing and CNC machining, allow for faster prototyping and production, significantly reducing lead times and enabling quicker time-to-market.
Applications of Precision Plastic Parts
Precision plastic parts are utilized across a broad spectrum of industries. Here are some key applications:
1. Automotive Industry
In the automotive sector, precision plastic parts are used for dashboards, interior components, and engine housing. Their lightweight nature contributes to improved fuel efficiency and reduced emissions.
2. Medical Devices
The healthcare industry relies heavily on precision plastic parts for medical devices, including syringes, surgical instruments, and diagnostic equipment, ensuring safety, reliability, and precision in critical applications.
3. Consumer Electronics
Plastic components are essential in consumer electronics, including smartphones, computers, and other devices. The precision of these parts enhances functionality and aesthetic appeal.
4. Aerospace
In aviation, the use of precision plastic parts helps in reducing weight while maintaining performance standards, leading to greater fuel efficiency and lower operational costs.
Choosing the Right Manufacturer for Precision Plastic Parts
Selecting the right manufacturer for your precision plastic parts is critical to the success of your project. Here are some factors to consider:
- Experience and Expertise: Look for manufacturers with extensive experience in producing precision plastic components in your specific industry.
- Technology and Capabilities: Ensure that the manufacturer utilizes advanced technologies and has the capability to meet your design specifications.
- Quality Control: Evaluate their quality assurance processes to guarantee that your parts will meet the required standards.
- Customer Support: Strong communication and customer support are vital for addressing any concerns or changes during the manufacturing process.
- Reputation: Research the manufacturer’s reputation through reviews and testimonials from past clients.
The Future of Precision Plastic Parts
As technology continues to advance, the future of precision plastic parts looks promising. Here are some emerging trends:
1. Sustainable Materials
With increasing environmental awareness, manufacturers are exploring sustainable and biodegradable plastics that minimize environmental impact without compromising quality and performance.
2. Smart Manufacturing
The integration of IoT and AI in manufacturing processes is leading to greater automation, improved precision, and real-time monitoring, ensuring consistent quality and efficiency.
3. 3D Printing Innovations
Advancements in 3D printing technology are enabling the production of highly customized and complex components, facilitating rapid prototyping and personalizing products for specific customer needs.
4. Enhanced Simulation Techniques
Modern simulation tools allow manufacturers to predict the performance and behavior of plastic parts before production, optimizing design and reducing wastage.
Conclusion
The role of precision plastic parts in modern manufacturing can’t be overstated. Their benefits, encompassing decreased costs, increased efficiency, and improved product quality, make them an indispensable component across various industries. As we look towards the future, innovations in technology are set to enhance the capabilities of precision plastic manufacturing further, paving the way for more sustainable, efficient, and high-quality production processes.
For businesses aiming to stay ahead of the curve, embracing the advancements in precision plastic part manufacturing will be key to maintaining competitive advantages in their respective markets.