The Impact of Plastic Mold Companies on Modern Manufacturing
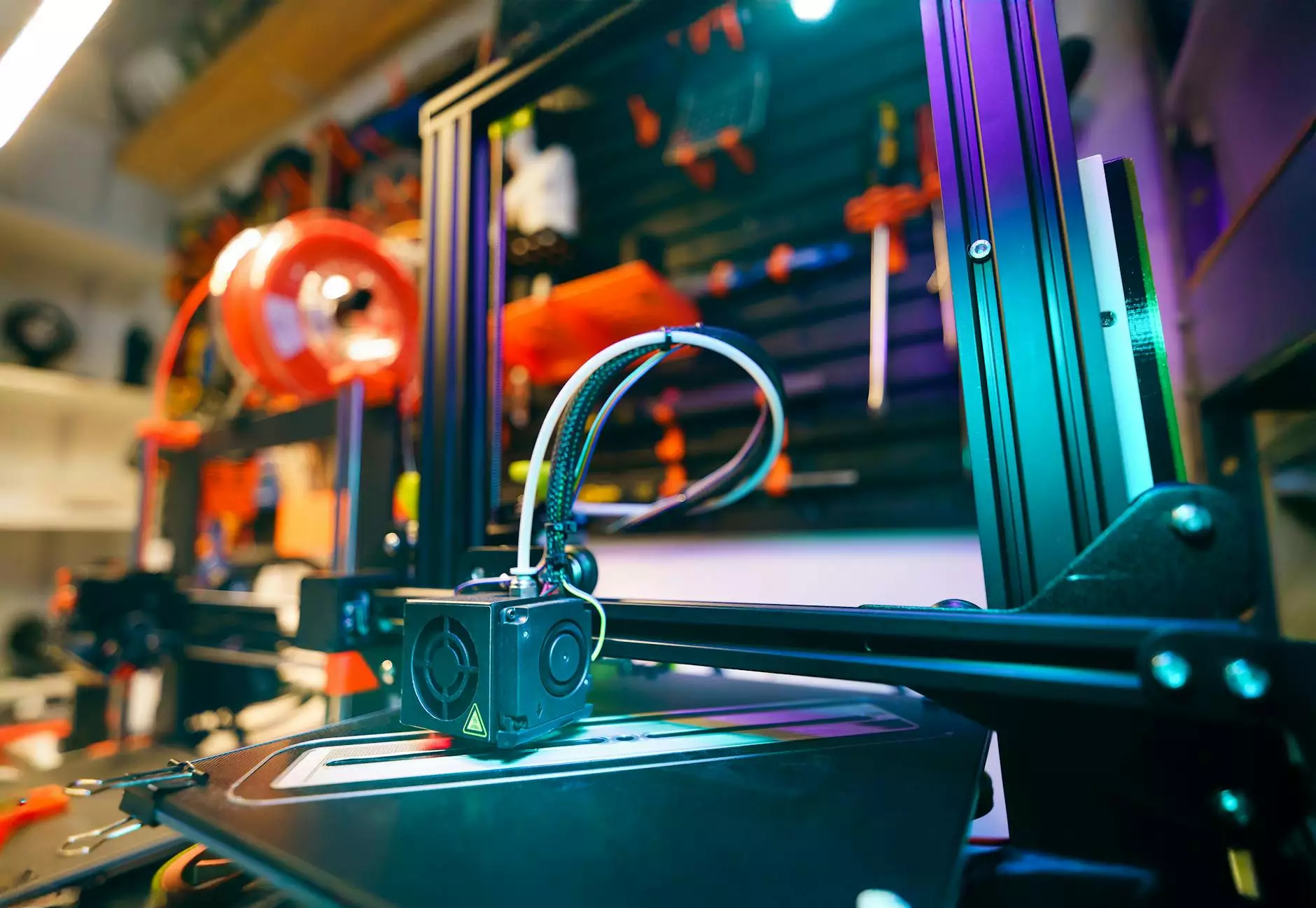
In today's fast-paced manufacturing industry, plastic mold companies play a pivotal role in producing a vast array of products that are vital for both everyday use and specialized applications. With their expertise in crafting molds tailored to specific needs, these companies have transformed the way products are designed, developed, and brought to market. This article delves into the importance of plastic mold companies, examining their processes, benefits, and the future of plastic manufacturing.
Understanding Plastic Molding
Plastic molding is a manufacturing process that involves shaping plastic into specific forms through the use of molds. It is a highly versatile technique that can be adapted for a variety of industries, including automotive, consumer goods, electronics, and healthcare. The primary methods of plastic molding include:
- Injection Molding: This is the most common method, where melted plastic is injected into a mold under pressure.
- Blow Molding: Used primarily for hollow objects like bottles, this process involves blowing air into a specially shaped mold.
- Rotational Molding: Here, a heated mold is rotated around multiple axes, allowing the plastic to coat the interior uniformly.
- Compression Molding: This method compresses plastic between two heated plates to form the desired shape.
The Importance of Plastic Mold Companies
Plastic mold companies are essential for several reasons:
1. Customization
One significant benefit of engaging with plastic mold companies is their ability to provide custom solutions. Each project can be tailored to meet specific requirements in terms of design, size, volume, and material properties. This level of customization enables companies to optimize their products for performance and cost-effectiveness.
2. Cost Efficiency
By investing in high-quality molds, businesses can significantly reduce production costs over time. Quality molds created by skilled plastic mold companies minimize defects and allow for higher production rates, which can lead to substantial savings.
3. Speed to Market
The rapid prototyping capabilities offered by plastic mold companies enable businesses to bring products to market faster than ever. Quick turnaround times on mold production mean that testing and development cycles can be shortened, allowing companies to respond swiftly to market demands.
Key Processes in Plastic Mold Manufacturing
The workflow within a typical plastic mold company encompasses several critical processes that ensure the creation of high-quality molds.
1. Design and Engineering
Every successful project begins with precise design and engineering. Using advanced software tools such as CAD (Computer-Aided Design), engineers collaborate with clients to create 3D models of the product and molds. This stage is crucial as it sets the foundation for all subsequent processes.
2. Material Selection
Choosing the right materials for the mold is essential for durability and product performance. Plastic mold companies typically work with various types of steel, aluminum, and composite materials, each offering advantages based on the specific application and lifespan required.
3. Machining and Fabrication
Once the design is finalized, the machining process begins. CNC (Computer Numerical Control) machines are used to precisely cut and shape the mold components. This precision is vital to ensure that the final product meets the required tolerances and specifications.
4. Assembly and Testing
After machining, the molds are assembled. Quality assurance tests are conducted to verify the mold's functionality and to ensure that it meets performance standards before it is approved for production.
Trends in the Plastic Mold Industry
The plastic mold industry is continuously evolving, driven by technological innovations and market demands. Some notable trends include:
1. Sustainable Practices
With growing environmental concerns, many plastic mold companies are adopting sustainable manufacturing practices. This includes using recycled materials for molds and optimizing production processes to reduce waste.
2. Automation and Smart Manufacturing
Automation through robotics and IoT (Internet of Things) technology enhances efficiency and precision in the manufacturing process. Smart manufacturing techniques allow for real-time monitoring and adjustments, leading to improved product quality.
3. Advanced Materials
The exploration of new materials, including bio-based plastics and high-performance polymers, is expanding the applications of plastic. Plastic mold companies are at the forefront of developing molds that can utilize these innovative materials effectively.
Future Outlook for Plastic Mold Companies
The future for plastic mold companies is filled with potential. As industry demands evolve, these companies will continue to play a vital role in innovation and manufacturing efficiency. Key areas for growth include:
1. Adapting to Industry 4.0
Embracing the principles of Industry 4.0 will allow plastic mold companies to enhance their operational effectiveness. This shift includes integrating AI for predictive maintenance, optimizing supply chains, and improving design processes.
2. Expanding Global Markets
As manufacturing increasingly becomes a global endeavor, plastic mold companies have the opportunity to expand their reach internationally. This globalization enables collaboration with diverse markets to share resources, technology, and expertise.
3. Focus on Quality and Compliance
Maintaining high-quality standards and compliance with international regulations is critical. Companies will need to invest in quality management systems and continuous training to meet the evolving expectations of safety and performance.
Choosing the Right Plastic Mold Company
When selecting a plastic mold company, several factors should be considered:
- Experience: Look for a company with a proven track record in the industry. Their experience often reflects their expertise in handling various projects.
- Technology: A company that invests in the latest technologies can offer better design and production capabilities.
- Customer Support: Strong communication and support throughout the project lifecycle is essential for a successful partnership.
- Portfolio: Reviewing previous projects can provide insight into the company’s capabilities and reliability.
Conclusion
In conclusion, plastic mold companies are integral to modern manufacturing processes, driving innovation and efficiency across many sectors. By specializing in the design and production of customized molds, they help businesses optimize their product offerings while reducing costs and time to market. As technology continues to advance and market needs evolve, these companies will remain pivotal in shaping the future of manufacturing. Engaging with a reputable plastic mold company can provide the competitive edge necessary to thrive in today’s dynamic business environment.