Understanding Final Drive Track Motors for Enhanced Performance
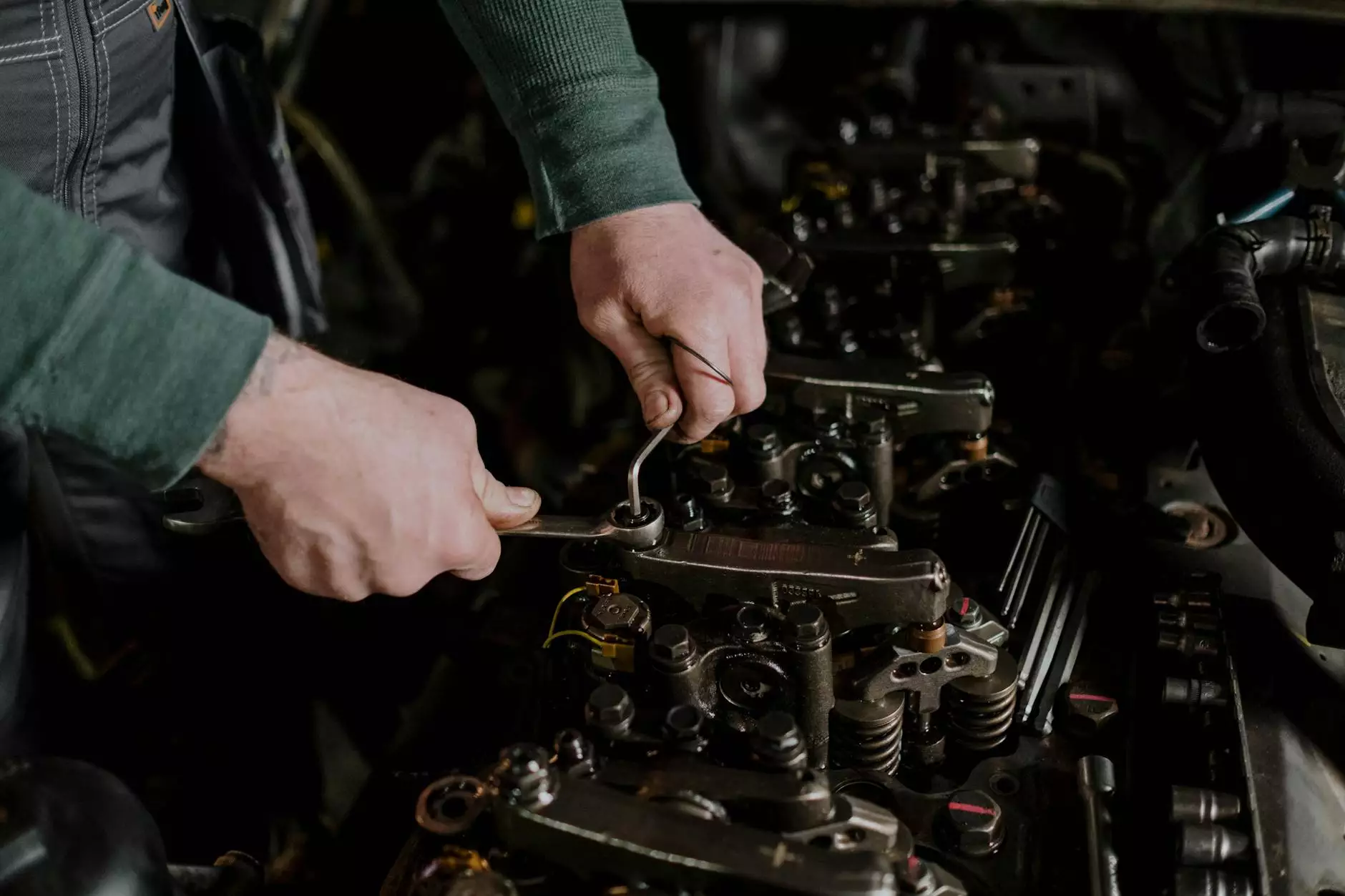
The world of machinery and automotive technology is extensive, with every component serving a critical role in enhancing performance and efficiency. Among these components, final drive track motors hold significant importance, especially in tracked vehicles such as excavators, bulldozers, and various other heavy equipment. In this article, we will delve deep into the functionality, features, benefits, and maintenance of final drive track motors.
What are Final Drive Track Motors?
Final drive track motors are hydraulic or electric devices that provide the necessary power to the tracks of heavy machinery. They enable tracked vehicles to move efficiently across different terrains while offering necessary torque and speed. These motors are crucial for the operation of excavators, skid steers, and similar equipment.
How Final Drive Track Motors Work
The functioning of final drive track motors can be comprehensively explained through the following steps:
- Power Generation: The motor receives hydraulic fluid or electrical power from the machine's engine or power unit.
- Torque Production: As the motor operates, it creates torque that is transferred to the final drive gear.
- Motion Transmission: The torque is transmitted through gears, ultimately rotating the drive sprockets that engage the tracks.
- Track Movement: This process enables the vehicle to move forward, backward, or turn, providing the necessary ground mobility.
Types of Final Drive Track Motors
Understanding the different types of final drive track motors can help in selecting the right one for your specific equipment:
- Hydraulic Final Drive Motors: Common in excavators and bulldozers, these motors use hydraulic fluid to create power. They offer high torque output and are suitable for heavy-duty applications.
- Electric Final Drive Motors: More prevalent in smaller machinery or electric vehicles, these motors are efficient and have lower operational costs. They provide precise control and are environmentally friendly.
- Planetary Gear Final Drives: This type incorporates a planetary gear system that distributes power effectively, optimizing torque and preventing undue wear.
Key Features of Final Drive Track Motors
When selecting final drive track motors, there are several key features to consider:
- Torque Capacity: Higher torque capacity allows the machine to perform heavy lifting and maneuvering tasks with ease.
- Speed Control: The ability to control speed is essential, especially in applications requiring precision.
- Durability: Motors must be rugged and designed to withstand harsh operating conditions, including dirt, vibration, and harsh weather.
- Efficiency: Efficient motors reduce fuel consumption and operational costs, significantly affecting overall project budgets.
Benefits of Using Final Drive Track Motors
The incorporation of final drive track motors in heavy machinery brings several advantages:
- Improved Traction: Better torque distribution allows machines to navigate uneven and slippery terrains with enhanced grip.
- Operational Efficiency: Well-designed final drive systems ensure optimal power usage, leading to lower fuel costs.
- Enhanced Performance: Provides the necessary force needed for demanding applications while maintaining control.
- Reduced Maintenance: Quality final drives are designed for minimal maintenance, reducing downtime and increasing productivity.
Applications of Final Drive Track Motors
Final drive track motors are utilized across a variety of industries and applications:
- Construction: For operating excavators, bulldozers, and track loaders in extensive construction projects.
- Agriculture: Used in ditching machines and other farm machinery to enhance land work efficiency.
- Mining: Essential for tracked vehicles operating in rugged mining environments where mobility is crucial.
- Dredging: Employed in dredgers that require powerful track movements for underwater excavation.
Choosing the Right Final Drive Track Motor
Selecting the appropriate final drive track motor for your machinery involves several considerations:
- Compatibility: Ensure the motor is compatible with your existing equipment to avoid installation issues.
- Performance Requirements: Assess the necessary torque and speed capabilities required for your tasks.
- Brand Reputation: Choose reputable brands such as manufacturers associated with Shop Hydraulic America known for their high-quality products.
- Cost-Effectiveness: Compare prices and evaluate the value offered in terms of performance and durability.
Maintenance Tips for Final Drive Track Motors
Regular maintenance can ensure longevity and optimal performance from your final drive track motors. Here are some essential tips:
- Regular Inspections: Frequently check for signs of wear, leaks, or damage, especially in hydraulic motors.
- Fluid Changes: Change hydraulic fluids as per the manufacturer's recommendations to ensure smooth operation and prevent overheating.
- Cleanliness: Keep the surrounding areas clean to prevent dirt and debris from entering the motor.
- Proper Handling: Handle the machinery with care to avoid stressing the motors during operations.
Final Thoughts
In the vast domain of machinery, final drive track motors serve as the backbone of tracked vehicles, providing them with the necessary power to navigate and perform efficiently in various environments. Understanding their functionality, benefits, and maintenance practices can help businesses make informed decisions while enhancing productivity.
As companies like Shop Hydraulic America continue to supply quality auto parts and supplies, including final drive track motors, businesses can confidently invest in equipment that keeps their operations running smoothly. By focusing on quality, compatibility, and performance, you can ensure that your machinery remains in optimal working condition, leading to greater efficiency and success in your projects.